Integrated Design for Improved Infection Control
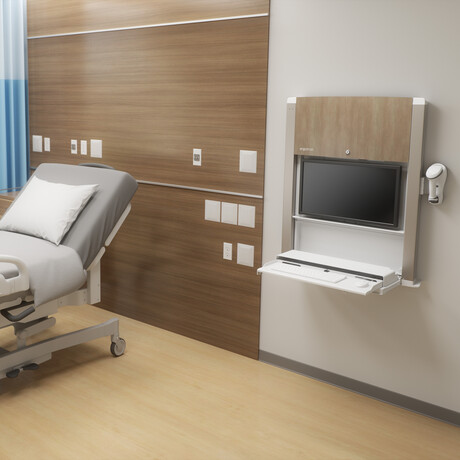
Ergotron was built on a desire to produce solutions that support the health and wellbeing of the individual and our vision is to be the world leader in improving how people work, learn, play and care for others.
Harry Sweere, the founder of Ergotron, designed computer workstations based on ergonomic principles and scientific anthropometric data for more than 20 years.
Harry’s legacy of innovation and commitment to ergonomics lives on in Ergotron’s mission of moving people forward with solutions that remove constraints for workers to thrive.
The commitment to health and efficient workspaces has driven Ergotron to be leaders in the field of designing solutions to enhance wellness and assist to create workspaces based on human centered design principles.
Why Design, Durability and Disinfectability are important
Within the Ergotron architecture all components have been considered and infection control is integrated into the very design and selection of materials for their disinfectability and durability. Effective infection prevention and control is central to providing high quality healthcare for patients and a safe working environment for those who work in healthcare settings.
Disinfectability of materials is essential to the ability of withstanding harsh chemicals and technology necessary to kill pathogens in healthcare settings.
The surfaces of the Ergotron Styleview range of medical workstations on wheels are treated with an antimicrobial finish, antimicrobial finishes and materials are simple to sanitise or are naturally germ resistant making it easier to maintain the high levels of cleanliness crucial in a healthcare environment.
Practically all hospital grade cleaning solutions can be used on all plastic and metal surfaces including quaternary ammonia compounds, ammonia enzyme cleaners, hydrogen peroxide bleach and alcohol solutions without surface damage.
The materials used in production are an important consideration as durability is key to preventing cracks, chips and flaws allowing dirt to accumulate making the surfaces difficult to clean.
All materials used in the Ergotron range are composed of aluminum, high grade plastic and zinc plated steel to support infection control. The unique cable management system conceals and organizes cords making cleaning easy and adds another layer to Ergotron’s commitment to products designed to meet the intense requirements of healthcare settings.
While the design, durability and disinfectability have all been considered, infection control administrators or epidemiologists should always be consulted for all cleaning procedures and processes.
For patient and caregiver safety the entire power system, in addition to the full cart are certified to UL/EN/IEC 60601-1 and CAN/CSA C22.2 No.601.1 M90. Also complies with EMI limits of FCC Part 15 Class A.
From the very first design when computers were a rarity in the workspace to today, where technology is integrated into virtually every aspect of the daily work environment, Ergotron has remained committed to the designing and creation of solutions that are fit for purpose.
For more information visit www.ergotron.com or call 0403 986 442.
Optimising surface cleaning chemical storage in healthcare
How are chemical dilution and dispensing equipment manufacturers helping healthcare managers to...
Medline introduces Namic Ready Set Kits
In the fast-paced healthcare industry, there is constant pressure to efficiently deliver...
How healthcare providers prevent infection
The spread of infection in the healthcare sector is an ongoing challenge for operators, so what...