Optimising surface cleaning chemical storage in healthcare
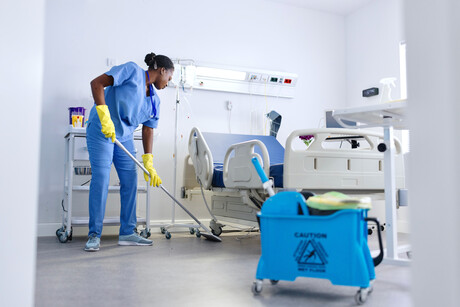
For operators in hospitals, care homes and other healthcare settings, preventing and controlling infection is a constant challenge, with outbreaks of bacteria such as MRSA and clostridium difficile placing additional strain on stretched staff and resources.
With cleaning and disinfection routines key to preventing the spread of viruses, a starting point is high-touch surfaces that can harbour bacteria. Although the scale of surface cleaning varies between low-risk (foyers, waiting rooms, offices and corridors) and high-risk (operating theatres and intensive care wards) areas, it’s critical that cleaning programme managers do not become complacent.
Examples include chair arms and seats in waiting areas as well as shared equipment such as keyboards, stethoscopes and ultrasound probes which are a major cause of cross contamination and must be wiped down regularly with disinfectant.
Meanwhile, call bells, grab rails, door handles and opening buttons/panels are touched countless times each day and are among the most likely surfaces to transmit infection.
In all toilet areas, from wards to public washrooms to staff facilities, a focus on obvious areas such as toilet bowls, urinals, sinks and floors should not mean that high-touch surfaces including taps, flush handles, dispensers, hand dryers, door handles and locks are neglected.
So how are chemical dilution and dispensing equipment manufacturers helping healthcare managers to minimise risk and protect patients, staff and visitors?
Achieving exceptional surface-cleaning standards relies upon chemical dispensers used for dosing concentrated and pre-mixed solutions into sinks, spray bottles, mop buckets and scrubber dryers being capable of combining precision and consistency with robustness and longevity.
In fast-paced, high-pressure environments such as emergency departments where excessive force and accidental collisions are common, a durable, impact-resistant dispenser housing helps to ensure repeatable, reliable performance while reducing the cost of maintenance, repair and replacement.
Budget limitations may make lightweight dispensers an attractive prospect, but while such systems are cheaper per unit they are also unreliable and commonly offer only a short lifespan, costing more in replacements over the long term compared with higher-quality, longer-lasting equipment.
When it comes to chemical storage, in many cleaning stations it’s common to see concentrated chemical containers such as 20-litre drums placed unbunded on the floor. As well as causing a potential leakage or trip hazard, this means staff are dosing detergent and other cleaning agents manually, exposing them to potentially harmful concentrated chemical.
This can be solved by integrating chemical storage and dilution, allowing operators to not only save space and make cleaning stations tidier and more presentable but also deliver essential health and safety benefits by keeping chemicals off the floor and avoiding possible spillage and trip hazards.
Such systems typically feature a cabinet-style enclosure where various-sized chemical containers can be stored and connected to the built-in dispenser. Lockable cabinets help to prevent theft and tampering and protect employees against exposure to aggressive concentrated chemicals.
It’s clear that establishing and maintaining exceptional surface-cleaning standards in healthcare is achievable with the right investment. Cleaning and hygiene equipment specialist SEKO knows this better than most as the company has been helping operators for decades with a dedicated range of chemical dilution, dispensing and dosing systems.
These include the modular ProMax dilution system, which allows users to dispense premixed chemical solutions into spray bottles, mop buckets and scrubber-dryers, as well as the fully compatible SekureMax and SekureDose storage cabinets.
SEKO’s latest dilution innovation is ProFlex, a dispenser designed with a venturi element that prevents chemicals mixing to ensure cleaning solutions are perfectly proportioned for optimal performance.
These systems and the rest of SEKO’s product range can be found at www.seko.com.
Medline introduces Namic Ready Set Kits
In the fast-paced healthcare industry, there is constant pressure to efficiently deliver...
How healthcare providers prevent infection
The spread of infection in the healthcare sector is an ongoing challenge for operators, so what...
There's more to decontamination than just disinfection…
Disinfection is often the main focus in medical device reprocessing, but is only one step of the...